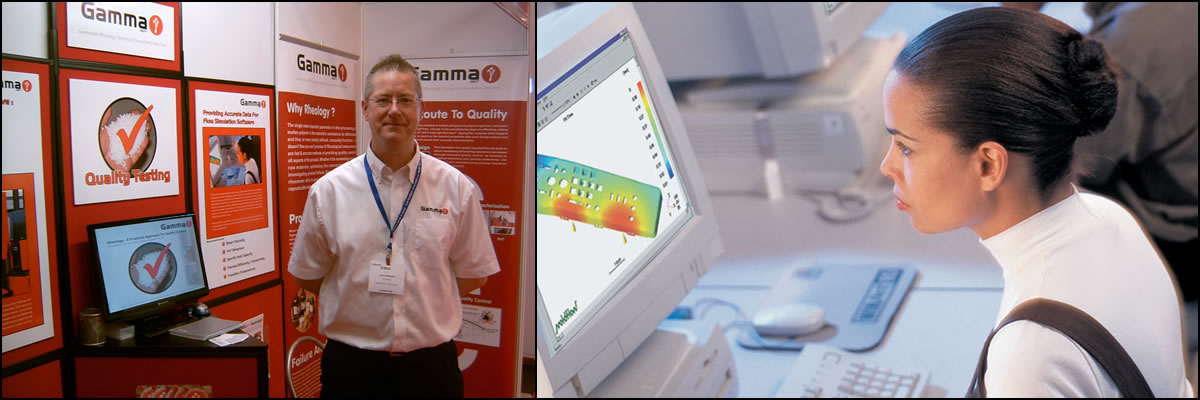
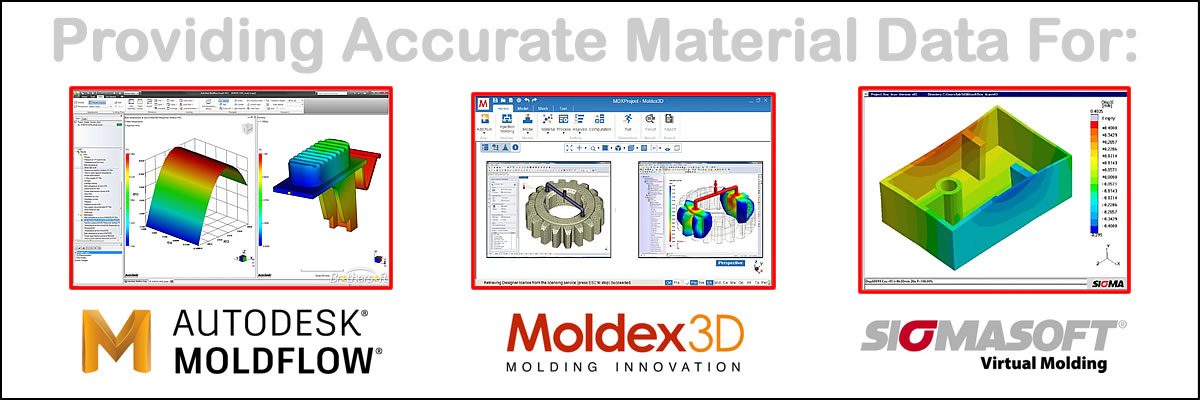
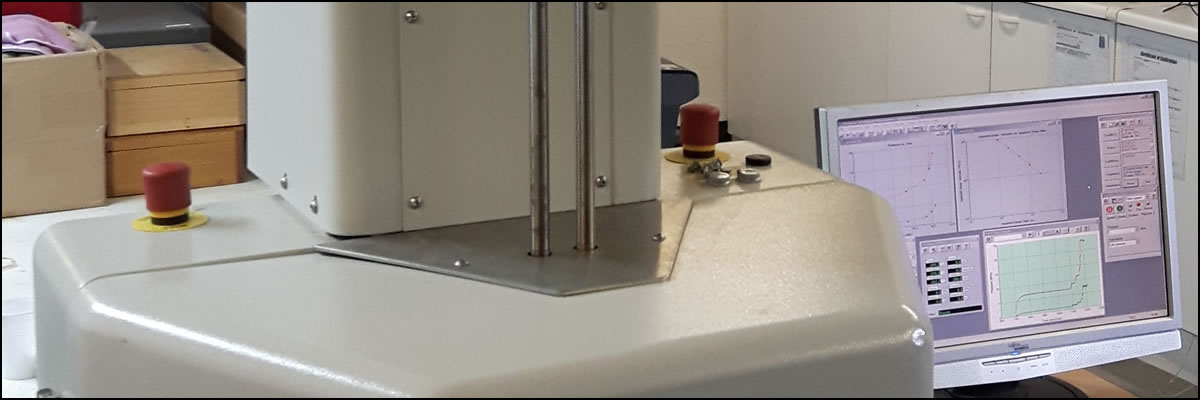
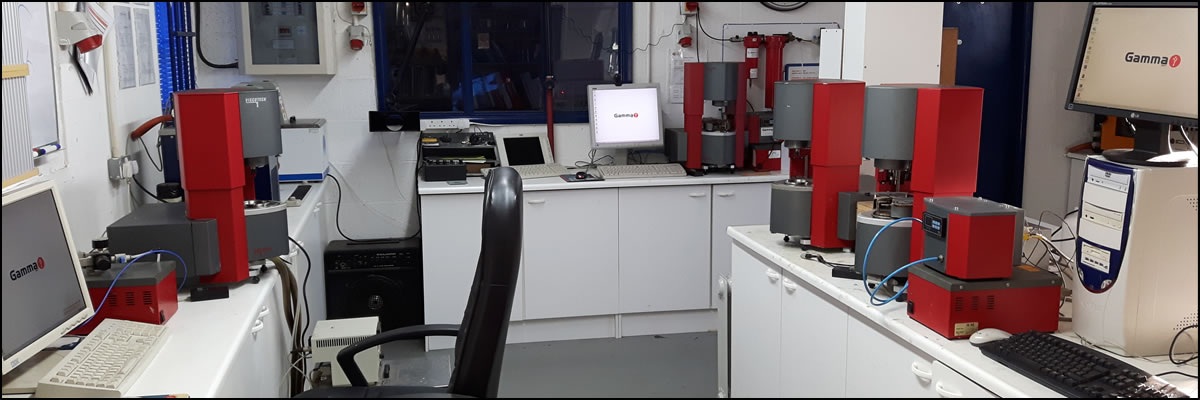
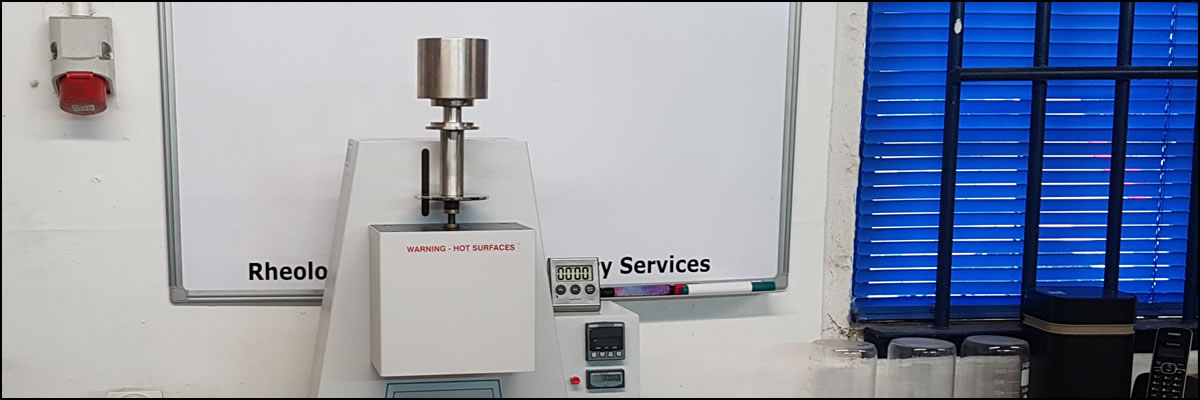
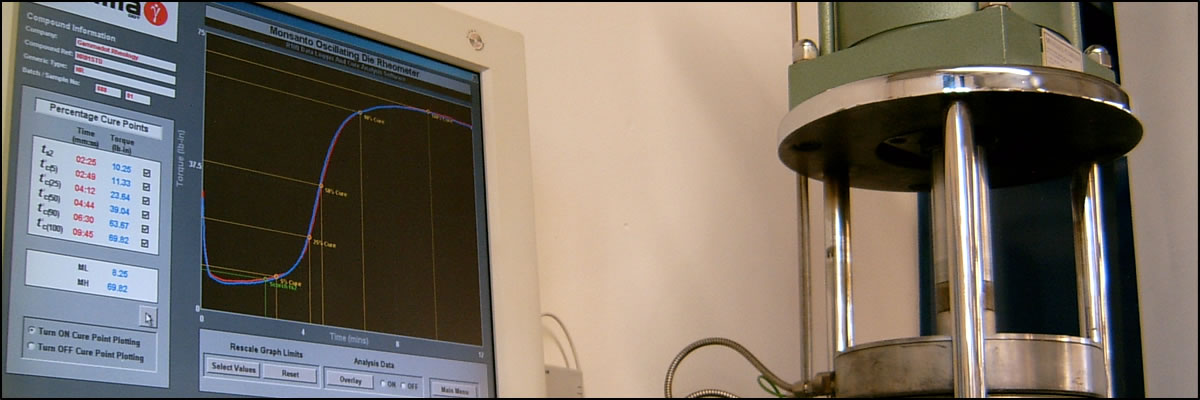
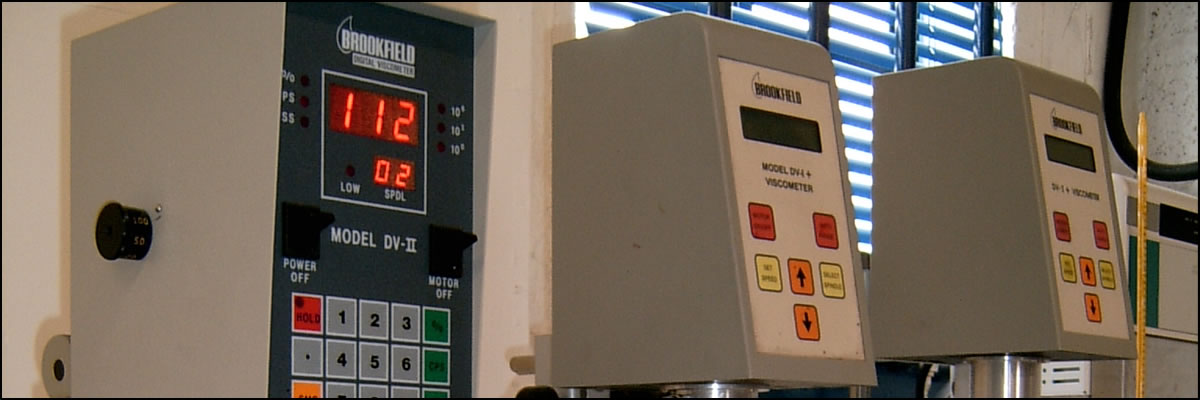
Welcome to Gammadot Rheology
Welcome to the web site of independent testing laboratory, Gammadot Rheology. Our skills and knowledge are based on over three decades of providing rheology and materials characterisation support to the plastics and rubber industries. In addition to the many polymer-orientated characterisation projects carried out over the years, we also have experience in characterising a variety of other fluids & semi-solids including: oils, greases, bitumen binders, food stuffs / additives, pharmaceutical creams & chemical solutions. Gammadot clients range from manufacturers to end users and cover a wide spectrum of sectors including: Medical, Automotive, Aerospace, Construction and Defence.
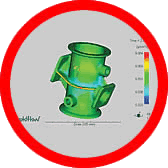
Product Design
Modern flow simulation software packages such as Moldflow, Moldex 3D and Sigmasoft 3D provide highly accurate models of the injection moulding process, but without the use of equally accurate material properties data, they are worthless – the old adage ‘rubbish in, rubbish out‘ holds true in process simulation. For this reason Gammadot offers comprehensive materials characterisation services supporting all of today’s leading packages at extremely attractive prices. Click HERE for more information on testing services.
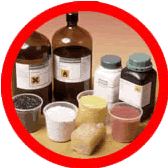
Quality Control
With ever increasing costs of raw feedstock, and processors under pressure to use more recycled materials in product manufacture, the importance of controlling & optimising today’s production processes is paramount. Key to minimising component reject rates is guaranteeing consistent material batches enter the production stream. Gammadot has many years experience tailoring quality control programmes to suit specific customer needs and therefore ensuring quality product by discriminating out of spec. materials offline. Read a past presentation HERE .
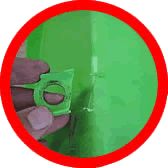
Failure Analysis
Rheological measurements play a key part in many plastics failure analysis projects, as techniques such as oscillatory rheometry are highly sensitive to changes in a materials structure and therefore can give first indications of failure cause: be it degradation due to inadequate drying of materials prior to processing, excessive thermal / shear history during conversion, the effects of service environment, or simply the wrong grade of material has been introduced into the process – oscillatory rheometry is an excellent first step towards solving the problem.