 |
Gammadot
Rheology Testing & Consultancy Services
Unit
5C, Leaton Industrial Estate, Bomere Heath. Shrewsbury. Shropshire.
SY4 3AP. UK
Tel: +44 (0)1939 291677 ...Email: enquiries@gammadot.com
|
|
Gammadot
Rheology Bi-Annual Newsletter - November 2010 |
Gammadot Reviews Cambridge Rheometer
Gammadot
Rheology, in partnership with Roy Carter & Associates, recently
visited Cambridge university to review the university-developed
Multi-Pass Rheometer (MPR).
This innovative instrument was designed & produced by the
department of Chemical Engineering and Biotechnology under the
leadership of Professor Malcolm Mackley. The MPR is in essence
a capillary rheometer with dual, opposing pistons which are independently
driven enabling a variety of rheological phenomena to be studied.
The modular design of the instrument enables a range of test cells
or capillary dies to be clamped between the two barrels giving
the facility to provide standard rheological measurements or perform
novel research investigating parameters such as:
 |
High
shear viscometry (Shear rates up to 160,000
1/s) |
 |
Optical
Flow Birefringence |
 |
Effects
of shear on crystallinity using X-ray Scattering |
 |
Pressure
Coefficient of Viscosity
(Pressure Dependence) |
 |
Bi-Axial
Extensional Viscosity |
 |
Thermal
/ Shear Stability Determinations |
This high-end rheometer is exclusively available from specialist
engineering firm, Strata
Technology Ltd - for more information relating to the
instrument and it's capabilities, take a look on the relevant
page of their web site here.
|
|
|
|
FOCUS
ON: Oscillatory Rheometry & Quality Control
In
the last Gammadot newsletter we demonstrated the inadequacies
of the melt flow rate instrument as a quality control
tool in favour of more versatile
equipment such as capillary or rotational rheometers.
There are those who still might ask, 'But
why use rheology for quality control?' For which the simplest
answer is: because the controlling factor in all polymer
conversion processes is the material's rheological behaviour
- if you can't deform & make the material flow, you
can't process it! The rheological response of a polymer
melt is also highly sensitive to material structure. A
rotational rheometer in oscillation mode (Oscillatory
Rheometry), can detect discrete changes in structural
properties, therefore affording an precise & accurate
method of providing quality control for all aspects of
the process. Whether it be screening incoming raw materials
to discriminate batch to batch variance, optimising the
conversion process through minimising the effects of thermal
& shear history, or determining the cause of degradation
in failed components, oscillatory rheometry can provide
this information in a fast & reproducible manner.
As
mentioned, Oscillatory rheometry measurements are
made utilising a rotational rheometer. This type
of rheometer is an extremely sensitive, yet robust
bench top instrument which is available in a number
of machine configurations. The measurement system
of the instrument is modular and therefore a wide
range of test parameters can be derived in conjunction
with the use of either plate / plate, cone &
plate or coaxial cylinder systems.
|
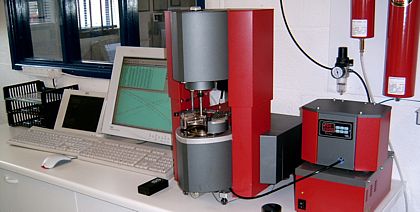 |
Some
examples of the type data that can be produced on the instrument
and their applications are demonstrated below:
Simple
'Go / No Go' quality control programmes
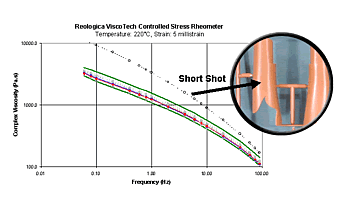 |
Controlling
quality of incoming batches of material is critical
to maintaining an optimised conversion process and
minimising reject rates. The graph on the left demonstrates
a simple 'Go / No Go' quality control programme
set up for an automotive components moulder who
operated a 'just in time' manufacturing regime.
The company had been experiencing problems with
variation in the properties of supplied batches
of Polypropylene, evident in fluctuating levels
of product reject rates - which threatened planned
delivery schedules. By characterising samples taken
from 'Good' & 'Bad' batches of material a simple
'process window' (the limits of which are indicated
by the green curves on the graph), was compiled
against which future batches could be compared -
enabling any incoming materials that fell outside
of the window to be rejected before entering the
production line.
Application
of Rheology to Failure Analysis |
Another
major application of oscillatory rheometry is the
support of failure analysis projects. The slide
on the right displays data produced as part of one
such project, carried out for an electrical connectors
manufacturer. Problems arose with a particular product
which had a brass fitting pressed into a central
boss within the moulding. This product was sourced
from two different manufacturing facilities - one
in Bulgaria which produced mouldings with no problems
and one in Poland which was producing components
that cracked upon pressing the brass insert into
position. The connector was moulded out of a glass-filled
PolyButylene Terephthalate (PBT) grade, a semi-crystalline,
hygroscopic (moisture sensitive) material. Sections
removed from both 'good' and failed components were
rheologically characterised and it could be seen
there was almost a full (log) decade drop in complex
viscosity across the measured frequency range between
the samples. This considerable decrease indicated
there had been a sharp reduction in molecular weight
due to degradation - chain scission probably being
a result of inadequate pre-process drying. |
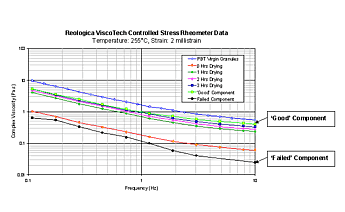 |
To confirm this theory, test specimens were injection
moulded after zero, one, two & three hours drying
in a vacuum oven @ a temperature of 135°C. Sections
of the dried mouldings and virgin granules were
measured and it could be seen that the viscosity
response of the undried (zero hours) moulding lays
closest to the failed sample's viscosity curve.
As predicted, as drying time was increased the level
of degradation decreased demonstrated by an increased
retention of properties. At the optimised drying
time for PBT of 3 hours @ 135°C it could be
seen the viscosity had risen to a level comparable
to that of the 'good' sample although interestingly,
after only one hours drying,
properties increased to a similar level.
|
Cure
Kinetics of Thermosetting Materials
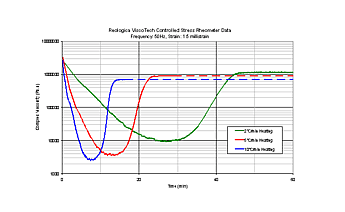 |
Due to the modular nature of the rotational rheometer
measurement system, disposable plate / plate systems
can be used to perform tests on curing and/or corrosive
materials. Measurements are usually carried out
isothermally at fixed strain & frequency as
a function time (Isothermal cure), or fixed strain
& frequency as a function of temperature, (reactive
viscosity measurements). The plot to the left depicts
the viscosity response of an Epoxy moulding compound
as a function of different heating rates. Running
as a function of temperature in cooling mode is
also excellent at determining phase transitions
in hot melt adhesives and investigating the effect
of changing ingredient ratios in compound trials.
|
Control
software for modern rotational rheometers are exceptionally
versatile. A useful function of software is the ability
to 'string' individual test programmes into a project
'macro'. The graph on the right is an example of this.
A manufacturer of products for the offshore oil industry
was encapsulating components in a large volume of
Polyurethane, for use in offshore applications. The
cured resin was required to reach a specific modulus
to ensure integrity of the moulding at the pressures
experienced in deep sea conditions. Full cure of the
moulding was not reached until almost 24 hours after
mixing and casting, and the cure kinetics passed through
three distinct phases: an initial exothermic reaction
which raised the temperature of the casting from 20°C
to 130°C, an hour at a constant 130°C (a result
of adiabatic heating), followed by an 18 hour slow
cooling phase.
This was easily replicated by using three test templates
joined together in a project macro. All templates
used the same fixed frequency & strain amplitude
with the first programme running a heating ramp from
20°C to 130°C @ a heating rate of 20°C/min
(to replicate the heat generated during the initial
exothermic reaction). The second programme was an
isothermal measurement @ 130°C for one hour, (simulating
adiabatic heating conditions), and the third programme
an extremely slow cooling ramp from 130°C to 20°C
over 18 hours (-0.102°C/min). |
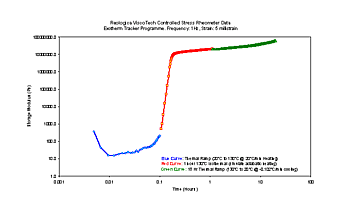 |
|
In addition to the small cross section of test programmes highlighted
above, the instrument is able to determine: thermal degradation
through melt stability studies, yield stress analysis, creep /
creep recovery and other standard rheology / viscometry techniques,
making the rotational rheometer an intrinsic part of a modern
day laboratories characterisation suite. Hopefully this short
piece has given an insight into the value of utilising controlled
stress rheometry in the solution of a variety of quality control
issues affecting processing, ranging from pre-process discrimination
of raw material to determining likely cause of failure in failed
products. Why don't you give Gammadot Rheology a call and discuss
your quality control needs today?
|
Back
to Top
Gammadot
Rheology exhibiting @ Interplas'11 |
With less than a year to the next tri-annual Interplas exhibition
at the national exhibition centre in Birmingham, Gammadot
Rheology is already looking to the design of an all new stand
layout to reflect the more accessible floor plan of our 2011
position. To celebrate next March's five year anniversary
of providing independent testing & consultancy to the
polymer industry, we will be giving away a raft of goodies
ranging from discount vouchers to a magnum of champagne! The
Gammadot stand (L14) is in a prime spot on the walk through
between the main hall and the PPMA exhibition. See you all
there!
|
Gammadot's
stand is the opposite side of the hall to 2008 - see
you there! |
|
|
Back
to Top
Gammadot
Service Flyer Download
|
For
further information about Gammadot Rheology's testing & consultancy
services, or if you have a specific problem / testing requirement
which you would like Gammadot to provide a solution to, please
contact us using the details at the top of the page or via the
enquiry form HERE.
You
have received this newsletter as a past customer, contact or because
Gammadot Rheology believes you are a company which may benefit
from our services, If you DO NOT
wish to receive any further email correspondence from Gammadot,
please reply to this message with the word REMOVE
in the subject bar, and we apologise for any inconvenience caused.
|

|